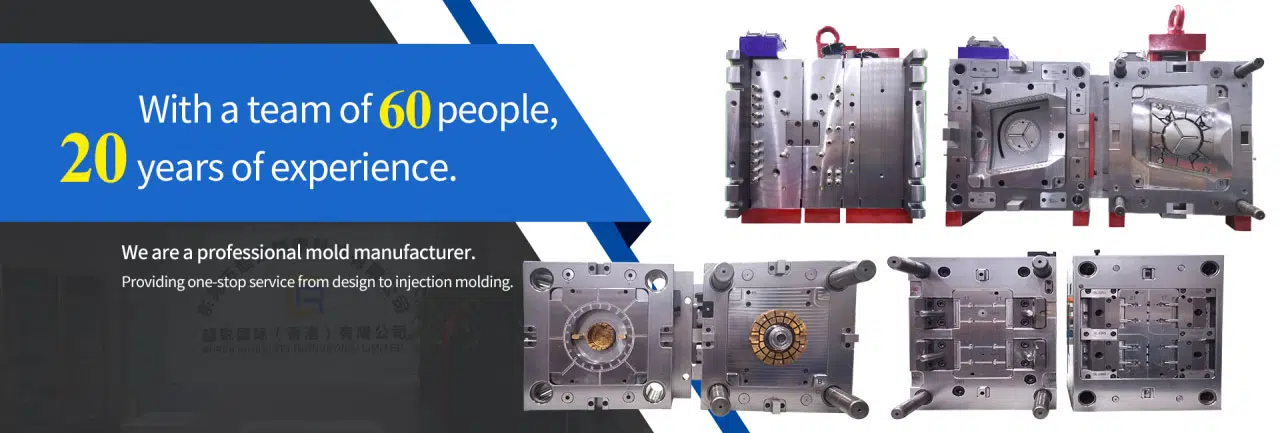
# High-Precision Machining: Achieving Unparalleled Accuracy in Manufacturing
Keyword: High-Precision Machining
## The Essence of High-Precision Machining
High-precision machining represents the pinnacle of manufacturing technology, where tolerances are measured in microns and surface finishes approach perfection. This specialized field combines advanced machinery, cutting-edge tooling, and meticulous processes to produce components with accuracy that was unimaginable just decades ago.
At its core, high-precision machining is about control – controlling every variable in the manufacturing process to eliminate deviations and ensure consistent, repeatable results. The applications span industries from aerospace to medical devices, where even the slightest imperfection can have significant consequences.
## Key Technologies Enabling Micron-Level Accuracy
Several technological advancements have made modern high-precision machining possible:
1. Advanced CNC Systems
Computer Numerical Control (CNC) systems have evolved to offer sub-micron positioning accuracy, with sophisticated feedback mechanisms that constantly monitor and adjust tool position.
2. Ultra-Precision Machine Tools
Specialized machine tools with thermally stable bases, vibration-damping systems, and air-bearing spindles create the stable environment needed for micron-level work.
3. Cutting-Edge Metrology
High-resolution measuring systems, including laser interferometers and coordinate measuring machines (CMMs), verify dimensions with nanometer-level precision.
4. Specialized Tooling
Diamond-tipped tools, micro-end mills, and other specialized cutting instruments maintain their edge geometry even under extreme precision demands.
## Applications Where Precision Matters Most
The demand for high-precision machining continues to grow across multiple industries:
Aerospace Components
Turbine blades, fuel system parts, and guidance system components all require exceptional dimensional accuracy to ensure safety and performance in extreme conditions.
Medical Devices
From surgical instruments to implantable devices, medical applications demand biocompatible materials machined to exacting specifications for proper function and patient safety.
Optics and Photonics
Lens mounts, mirror substrates, and laser components require surface finishes and dimensional tolerances that only high-precision machining can provide.
Semiconductor Manufacturing
The equipment used to produce microchips contains numerous precision-machined components that must maintain stability at atomic scales.
## The Future of Precision Manufacturing
As technology advances, the boundaries of high-precision machining continue to be pushed further. Emerging trends include:
- Integration of artificial intelligence for real-time process optimization
- Development of new ultra-hard materials for cutting tools
- Advancements in in-process measurement and adaptive control
- Miniaturization enabling machining at the nanoscale
The pursuit of ever-greater precision drives innovation across the manufacturing sector, creating new possibilities for product design and performance. As tolerances shrink and surface quality improves, high-precision machining will continue to enable breakthroughs in technology and science.