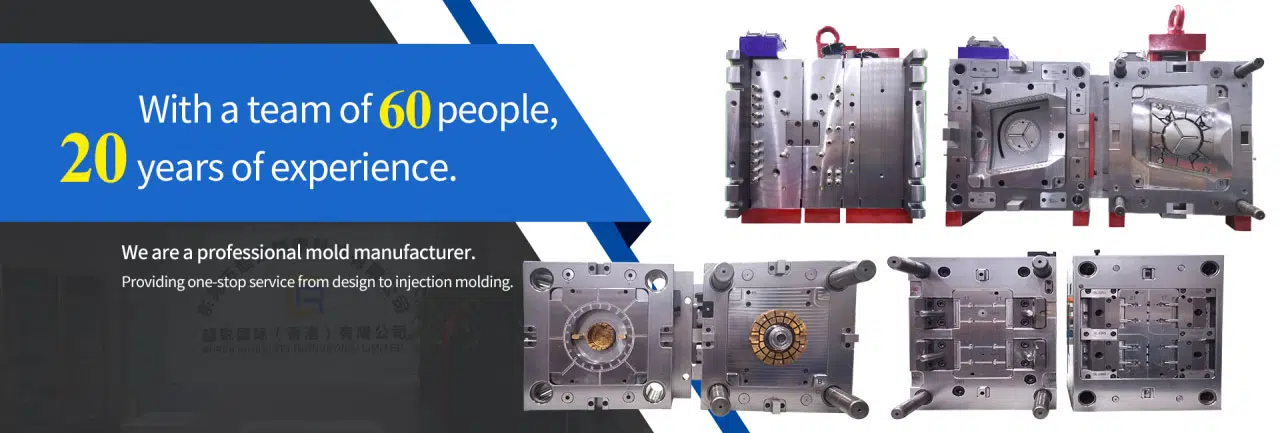
# Anodizing Process for Aluminum Alloys
## What is Anodizing?
Anodizing is an electrochemical process that converts the metal surface into a durable, corrosion-resistant, and decorative anodic oxide finish. This process is most commonly applied to aluminum alloys, though other metals like magnesium and titanium can also be anodized.
## The Anodizing Process Step by Step
### 1. Cleaning
The aluminum parts are thoroughly cleaned to remove any dirt, grease, or other contaminants. This is typically done using a combination of alkaline cleaners and acid rinses.
### 2. Etching
The parts are then etched to remove surface imperfections and create a uniform surface texture. This step often uses sodium hydroxide solution.
### 3. Anodizing
The actual anodizing occurs in an electrolytic bath where the aluminum acts as the anode. The most common electrolytes used are:
– Sulfuric acid (most common)
– Chromic acid
– Oxalic acid
### 4. Coloring (Optional)
After anodizing, the porous oxide layer can be dyed various colors. Common coloring methods include:
– Electrolytic coloring
– Dip coloring
– Integral coloring
### 5. Sealing
The final step involves sealing the porous oxide layer to improve corrosion resistance. This is typically done using hot water or steam treatment.
## Benefits of Anodizing Aluminum Alloys
Anodizing offers numerous advantages for aluminum components:
– Enhanced corrosion resistance
– Improved wear resistance
– Better adhesion for paints and adhesives
– Electrical insulation
– Aesthetic appeal with various color options
– Environmentally friendly process
## Applications of Anodized Aluminum
Anodized aluminum finds use in numerous industries:
– Architectural applications (window frames, building facades)
– Automotive components
– Aerospace parts
– Consumer electronics
– Cookware
– Medical equipment
## Types of Anodizing
There are several types of anodizing processes:
### Type I – Chromic Acid Anodizing
This process uses chromic acid and produces a thinner coating than other methods. It’s often used for aerospace applications.
### Type II – Sulfuric Acid Anodizing
The most common method, producing coatings from 1.8 to 25 microns thick. Suitable for most industrial applications.
### Type III – Hard Anodizing
Produces much thicker and harder coatings (up to 125 microns) for applications requiring extreme wear resistance.
## Factors Affecting Anodizing Quality
Several factors influence the quality of the anodized finish:
– Alloy composition
– Surface preparation
– Electrolyte concentration
– Temperature
– Current density
– Processing time
## Maintenance of Anodized Aluminum
While anodized aluminum is highly durable, proper maintenance can extend its lifespan:
– Regular cleaning with mild soap and water
– Avoiding abrasive cleaners
Keyword: Anodizing
– Prompt removal of contaminants
– Periodic inspection for damage
The anodizing process transforms aluminum alloys into more durable, attractive, and functional materials suitable for a wide range of applications. By understanding the process steps, benefits, and maintenance requirements, manufacturers and end-users can make informed decisions about using anodized aluminum components.